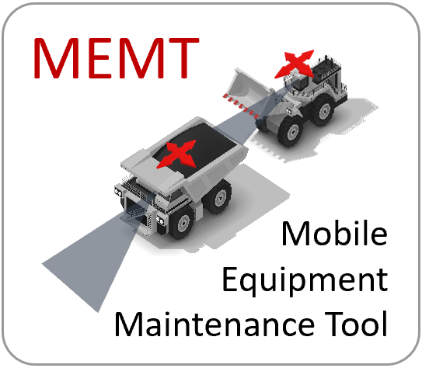
Objectives of the service
The objective of MEMT is to get situational awareness of the mining operation & working environment. Through KPIs and specific machinery information people are able to act and thus to ensure a proper machine performance and health condition.
The system especially provides information on the working conditions and working environment of those machines under harsh mining conditions by bringing together computer vision and sensor data analysis to empower its users to really see what´s going on in their mines.
Users and their needs
MEMT is a tool addressed to mining companies active in the extraction and processing of raw materials from open-pit mines to quarries, where mobile heavy machinery is the main factor for value creation. More specifically, it addresses the mine managers and foremen of such operations, that are looking to improve the efficiency of their sites and need actionable insights for taking informed, business-oriented decisions. Their need is to improve the efficiency of their operations, meaning either to increase the production keeping the cost level, or to keep production level but decrease the operating costs. For extraction and haulage of mineral resources, this means controlling the overall equipment efficiency, the mass-flow and the production, by having an overview, but also by having the means to go in details and investigate.
Mine managers have pointed out some specific issues that they currently face, such as productivity drops of 10-15% after periods of bad weather, due to road deterioration increasing the transport cycle times. Or that they experience lower excavation performance when they work with coarse or blocky material, but they don’t know when, where and how to adjust the blasting parameters.
The problem is that most small and medium sized mines are still relying on pen and paper for solving such challenges and therefore don’t have enough data for a good traceability of the material and the equipment throughout the mining processes. Furthermore, when they decide to switch to digital solutions, products and services that are available on the market are mostly OEM driven and mainly address large mines, which makes these solutions too expensive for smaller mine operators and unsuitable for mixed or subcontracted equipment fleets.
Service/ system concept
MEMT is an intelligent supporting tool, dedicated to mine managers and foremen of small and medium sized operations, consisting of a plug & play hardware module and a web-frontend that provides insights on specific mining processes.
The concept of the system is to collect, correlate and analyse data about the mobile heavy machinery in the mine, the working conditions and the environment.
For data collection a self-developed hardware is installed in the driver´s cabin of mobile heavy machinery. This relies on a collection of smart sensors, the most important ones being the global navigation satellite system (GNSS) receiver for location data and an inertial measurement unit (IMU) for data on spatial movements. In addition, a camera module provides images on road status, blasted and excavated material, machine components like bucket and teeth, surrounding equipment and people.
The datasets are collected, transmitted to the server and synchronized with the datasets coming from all other machines active in a specific operation, allowing to determine the movement patterns of these machines and processual interactions between them.
For data transmission the tool relies on terrestrial mobile networks and on SatCom, for areas where no terrestrial communication is available.
Finally, the system provides real-time relevant information via a user-centric web front-end. This allows the user to act upon in order to assure a good performance of the machines, and on the long-term, the conservation of the health condition of the fleet.
In other words, MEMT notifies the user about situations in the daily operation that could negatively impact machine performance and health when they have a frequent occurrence or are maintained over long periods of time (for example deteriorated haulage routes, narrow benches, steep curves and slopes, predominantly blocky material etc.).
Based on the information automatically collected by MEMT and analysed with the help of artificial intelligence, MEMT provides situational awareness to the mine management, who can take mitigation measures.
Space Added Value
Location data (GNSS) is the main connection point of all data sets used by MEMT and is the basis of all other correlations and analysis needed for identifying and classifying events and for providing the metrics and KPIs to the end-user.
One of the most requested functionalities by the customers is the display of map-supported data in a web-frontend, for an easy overview and comprehension, which again translates into the need for georeferenced data.
Satellite Navigation is the main space asset used by MEMT – GNSS is the backbone of the datalogger. The value that SatNav brings to our solution is that it enables a relationship between machine data and its environment, and together with time references (timestamps) it makes possible the automated combination of machine sensor data and computer vision of working environment. This allows us to be first movers in bringing such a use case to the mining industry.
In addition to this, SatCom is considered for data transmission, as an alternative to terrestrial communication, in areas where this type of connectivity is not available.
Current Status
abaut GmbH conducted the MEMT Kickstart Activity as part of the ESA’s BASS Kick-start programme under the thematic call on Predictive Maintenance. This was done in close collaboration with an industrial mining partner.
This interaction resulted in a detailed and customer-driven definition of the use-cases of MEMT, which were then reflected in the system functionalities and architecture.
Working along-side an industrial partner also made possible the proof of concept of critical aspects of the system in a relevant environment. The positive feedback from the project partner came as a validation and determined us to continue with the development of MEMT through a follow-on demonstration project.