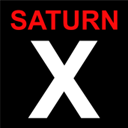
Objectives of the service
SaturnX addresses the critical need for safe, efficient and continuous monitoring of offshore wind farms, a challenging environment where traditional inspections require technicians to climb turbines or operate costly vessel-based drones. These methods can be hazardous, limited by weather conditions and demand significant resources. SaturnX offers a fully autonomous, remotely operated drone solution that inspects wind turbines directly from a Launch/Recovery/Recharge Platform (LARRP) stationed offshore and operated from an onshore Control Centre.
Equipped with high-resolution sensors, including RGB and thermal cameras, SaturnX captures detailed imagery of turbine towers, blades, and nacelles, identifying structural issues like cracks, moisture and sub-surface integrity. SWAP-optimised satellite communication technology enables Beyond Visual Line of Sight (BVLOS) control, transmitting real-time data to onshore personnel for immediate analysis and action.
SaturnX streamlines the inspection process, reduces operational downtime and lowers costs for wind farm operators by eliminating the need for on-site personnel. By developing a reliable data acquisition and transmission system with a focus on safety, high image quality and autonomous operation, SaturnX enhances asset management and increases the operational lifespan of wind turbines, contributing to a more sustainable energy sector.
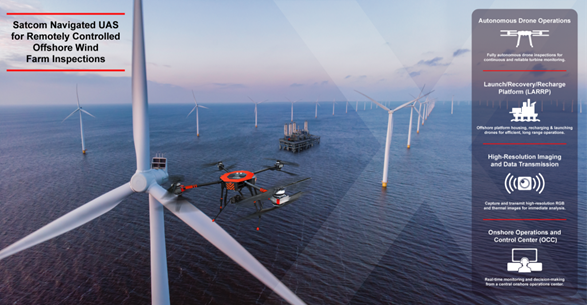
Users and their needs
The primary user communities for SaturnX are offshore wind park (OWP) operators, O&M service providers and offshore oil & gas platform operators. These users require precise, efficient, and cost-effective inspection solutions for monitoring wind turbines and oil & gas platforms in challenging offshore environments, where maintenance and monitoring costs are substantial. Key needs include:
-
Reliability: Dependable systems that minimise downtime and ensure uninterrupted energy production, especially with a growing dependence on offshore wind energy. A longer system life cycle for turbines/ blades is expected.
-
Cost-efficiency: Reduced inspection costs aligned with operational/maintenance budgets, currently estimated at around EUR 85 million per 1 GW of output.
-
Safety: Reducing the need for human presence in hazardous offshore conditions for prioritised personnel safety.
-
Digital data: As opposed to manual inspections, SaturnX provides entirely digital data in high quality, with accurate repeatable missions for future comparison.
-
Flexible inspection intervals: Less dependence on weather conditions/crew availability as well as a higher frequency of inspections shall be available.
Challenges to meeting these needs include ensuring robust satellite communications for BVLOS functionality, integrating AI-driven inspection capabilities, battery life & sustainability, and achieving scalable, real-time data processing to support predictive maintenance in high-risk environments.
Service/ system concept
SaturnX provides wind farm operators with a powerful, autonomous drone-based system to inspect offshore wind turbines efficiently and safely. By using drones equipped with high-resolution cameras and sensors, the system collects detailed digital data on turbine conditions without needing manual inspections. This data is then transmitted to an onshore operations centre (OCC) through satellite links, ensuring real-time monitoring and quick decision-making from anywhere.
The system consists of autonomous drones housed in offshore "garages" (containerised charging and launch stations) near wind farms. The drones are programmed to inspect turbines, capture data, and return to recharge autonomously. The OCC operators oversee operations, process the data with AI (Artificial Intelligence), and can step in for manual navigation if required.
System Architecture
-
Fully-fledged simulation environment and system (realistic environment, operational/technical digital twin)
-
Containerised LARRP for remote operation from onshore OCC
-
Operating software for LARRP
-
Customised maritime drone with satcom connectivity
-
Drone navigation sensor suite for obstacle avoidance, precision landing and BVLOS operations
-
OCC infrastructure with all BVLOS functionalities and redundancies
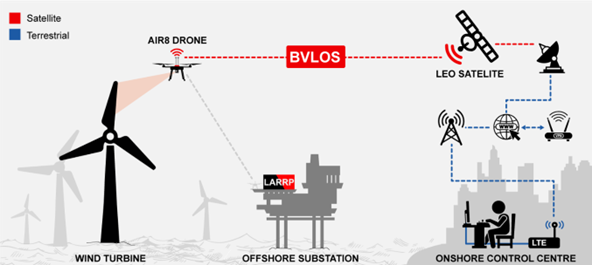
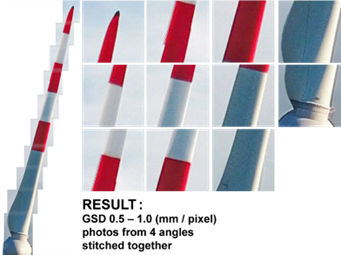
Space Added Value
SaturnX utilises advanced space assets, primarily satellite communication (SatCom) systems, including GEO and LEO satellites, to enhance offshore wind farm inspections. By integrating these satellite systems, SaturnX ensures reliable, real-time data transmission from drones positioned offshore to the onshore control centre (OCC), regardless of location or weather conditions. This capability is crucial for conducting inspections beyond visual line of sight (BVLOS), a significant improvement over traditional methods that rely on manual inspections and direct visual monitoring, often resulting in higher costs and longer downtime.
Combining satcom with autonomous drone technology (SatNav) allows for efficient data capture, high-resolution imaging, and automated reporting. This approach not only reduces operational costs by up to 90% but also enhances safety by eliminating the need for personnel to conduct dangerous inspections on turbines. Compared to existing competitors, who may rely solely on manned vessels or limited communication methods, SaturnX provides a more sustainable, efficient, and safe solution, contributing to net-zero emissions goals in offshore wind energy operations. Overall, the integration of space assets in SaturnX significantly boosts operational efficiency and reliability while minimising environmental impact.
Current Status
Following the activity kick-off in November 2024, SaturnX has advanced with key developments completed, including a robust baseline for the simulation environment and digital twin for service optimisation. Satellite communication tests were successfully concluded in collaboration with partners, confirming reliable BVLOS (Beyond Visual Line of Sight) capabilities via GEO and LEO systems. A customised AIR8 Medium Lifter drone with advanced sensors and satellite connectivity was integrated and initial autonomous recharging (LARRP) prototypes were tested.
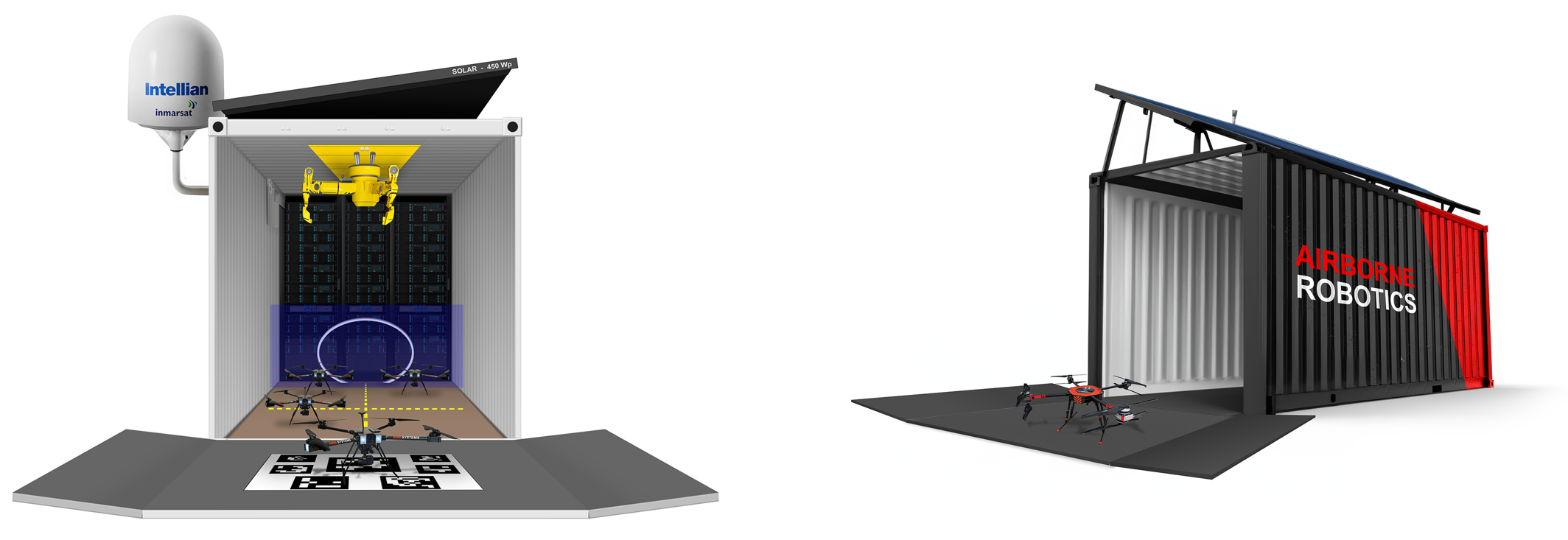
Currently, we are conducting pilot tests in an offshore wind farm environment to validate autonomous inspection operations and are in the design phase of LARRP system’s main housing container.
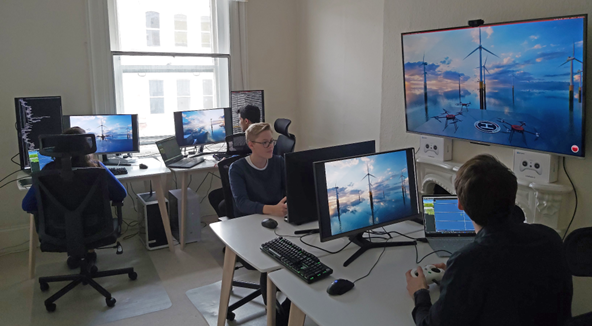
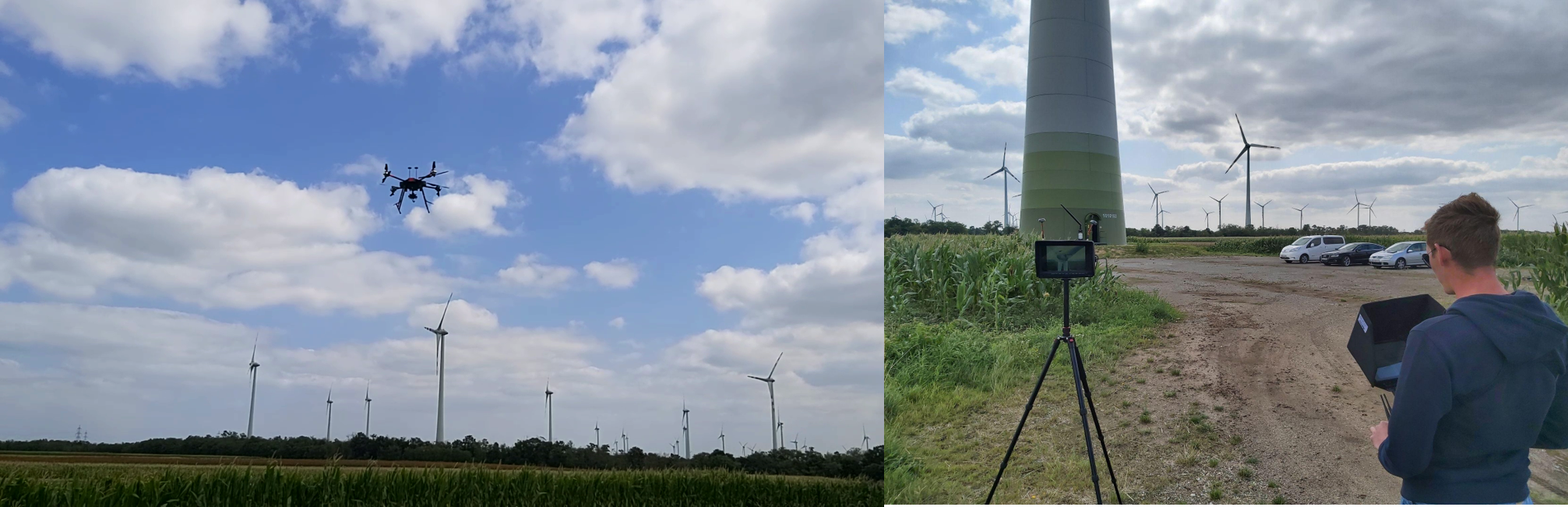
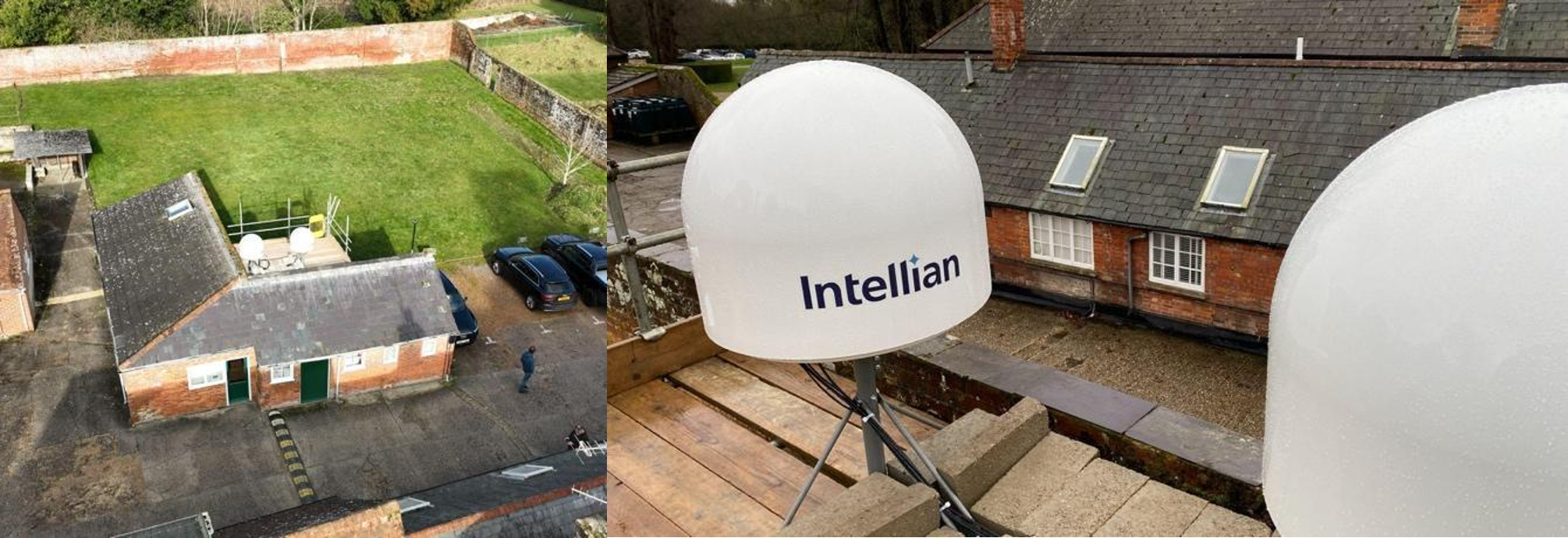
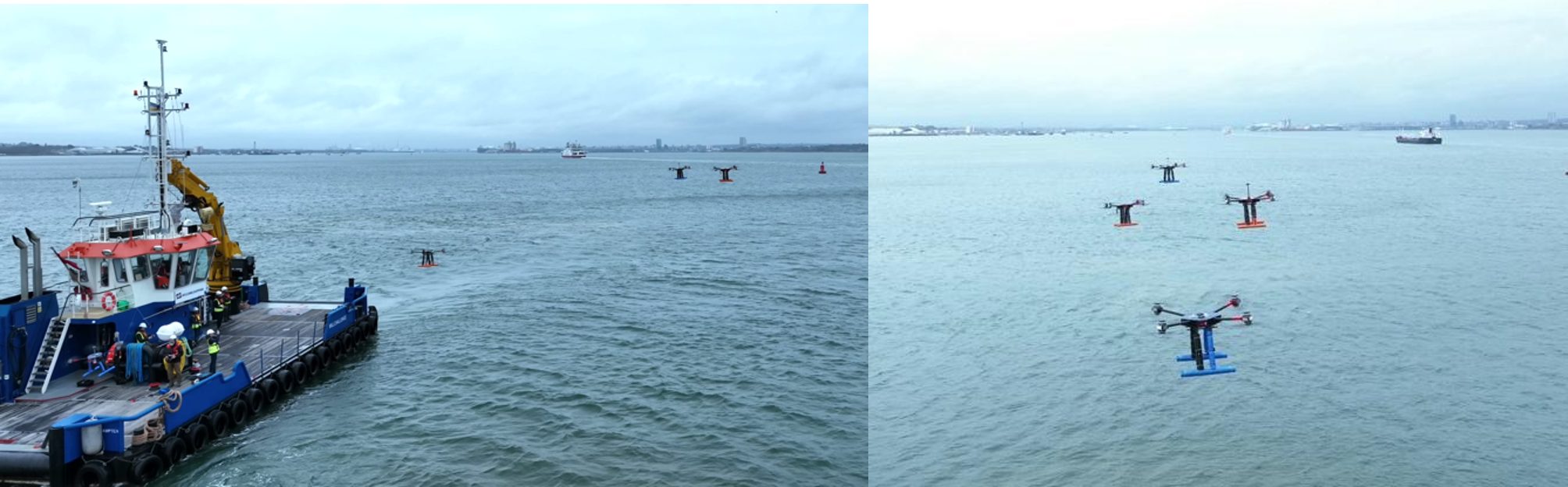
Upcoming activities include a series of test flights to optimise navigation and data collection protocols, regulatory compliance consultations to pursue a CAA BVLOS exemption, and engagement sessions with wind farm operators to demonstrate the digital twin and gather operational feedback for the turnkey service.
The next activity milestone is the Baseline Design Review, currently foreseen in the beginning of February 2025.
Prime Contractor(s)
Subcontractor(s)
